Bearings are indispensable in the world of engineering and manufacturing, especially in precision machining where high performance and longevity are essential. From supporting smooth rotational motion to minimizing friction, bearings play a vital role in ensuring that machinery operates efficiently and reliably. In this extended exploration of bearing types and their uses, we’ll dive into some of the most critical categories and their specific applications. Whether you’re an engineer, a machine operator, or simply curious about the world of mechanical components, understanding these elements is key to appreciating their role in modern machinery. so, let’s find out What Are Bearings and Why Are They Essential in Industrial Machinery?
1. Ball Bearings 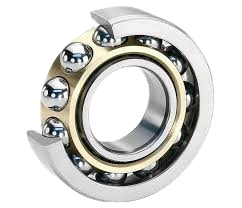
Ball bearings are perhaps the most well-known type of bearing, and they are revered for their simplicity and versatility. Consisting of small metal or ceramic balls placed between an inner and outer race, these bearings are designed to reduce friction while supporting both radial and axial loads.
- Key Features:
- Low friction: The smooth balls enable low rolling resistance.
- High rotational speeds: Ball bearings can operate at higher speeds compared to other types.
- Versatility: They handle both thrust (axial) and radial loads, making them adaptable to a wide range of conditions.
- Common Applications:
- Electric Motors: Ball bearings are the go-to option in electric motors, where efficiency and smooth operation are paramount.
- Automotive Applications: They are also found in gearboxes and steering systems, enabling vehicles to function smoothly.
- Consumer Goods: Hard drives, fans, and various household appliances rely on ball bearings to ensure quiet, reliable operation
2. Roller Bearings 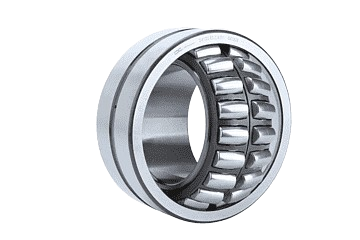
Roller bearings, as the name suggests, use cylindrical rollers instead of balls. This unique design allows them to support heavier radial loads, making them perfect for industries that demand robust, load-bearing capacity.
- Key Features:
- Higher Load Capacity: The line contact between the rollers and races allows these bearings to support much heavier loads than ball bearings.
- Radial Load Focus: These bearings are primarily used in applications where the load is perpendicular to the shaft.
- Common Applications:
- Industrial Machinery: Found in conveyor belts, large gearboxes, and industrial equipment, roller bearings are essential for handling the high stress these machines endure.
- Construction Equipment: The heavy-duty nature of roller bearings makes them indispensable in construction machinery such as bulldozers and cranes, where reliability under heavy loads is critical
3. Tapered Roller Bearings 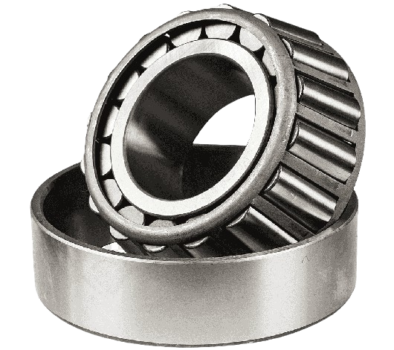
One of the most specialized types, tapered roller bearings feature rollers that are shaped like truncated cones, allowing them to handle both radial and axial loads simultaneously. Their tapered design spreads out the load over a larger area, which increases their load-bearing capacity.
- Key Features:
- Dual Load Handling: Tapered roller bearings are ideal for applications that encounter both thrust and radial forces.
- High Durability: Their design is robust, ensuring long operational life even in challenging conditions.
- Common Applications:
- Automotive Wheel Hubs: These bearings are often found in vehicle wheel hubs, where they manage the combination of axial and radial forces encountered during turning and acceleration.
- Aviation and Railways: Given their load-carrying capacity and precision, tapered roller bearings are frequently used in aviation landing gear and train axles
4. Needle Bearings 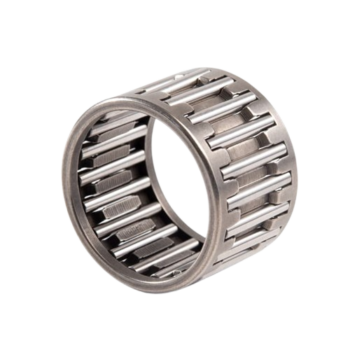
Needle bearings are a subtype of roller bearings but use long, thin cylindrical rollers. Despite their small footprint, they offer exceptional load-bearing capacity and are perfect for applications where space is a premium.
- Key Features:
- Compact Design: Their thin rollers allow for high load capacity in tight spaces.
- Lightweight: Needle bearings are often lighter than other roller bearings, making them ideal for weight-sensitive applications.
- Common Applications:
- Automotive Transmissions: Needle bearings are commonly found in transmissions and universal joints, where compactness is as important as load-bearing.
- Two-Wheeled Vehicles: Motorcycles and bicycles use needle bearings in their suspension systems for smooth performance under dynamic loads
5. Magnetic Bearings 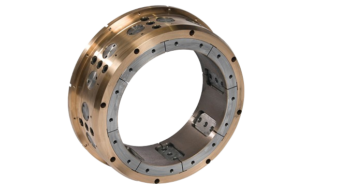
An advanced and unique type of bearing, magnetic bearings leverage electromagnetic forces to suspend moving parts, allowing for frictionless operation. While they are more costly and complex than mechanical bearings, they offer significant advantages in specialized applications.
- Key Features:
- No Physical Contact: Magnetic bearings operate without any physical contact, meaning there is no wear and tear due to friction.
- High-Speed Operation: These bearings are ideal for high-speed machinery where traditional bearings might fail due to heat buildup or friction.
- Common Applications:
- Turbomachinery: Magnetic bearings are used in high-speed turbines, compressors, and energy generation systems where precision, low maintenance, and long lifespan are critical.
- Aerospace: In aviation and space exploration, where precision and durability are crucial, magnetic bearings are invaluable
6. What are Thrust Bearings 
Thrust bearings are designed to manage loads applied parallel to the axis of rotation. There are various types of thrust bearings, such as ball thrust bearings and roller thrust bearings, each suited to different load capacities and applications.
- Key Features:
- Axial Load Handling: Unlike other bearings, thrust bearings are specialized to manage axial forces.
- Variety of Configurations: Thrust bearings come in various configurations to handle different levels of axial forces, from lightweight to heavy-duty applications.
- Common Applications:
- Automotive Transmissions: Thrust bearings play a vital role in managing the axial forces in transmission gears.
- Marine Propulsion Systems: These bearings are often used in ship propellers to handle the immense axial forces created during propulsion
7. What are Fluid Bearings 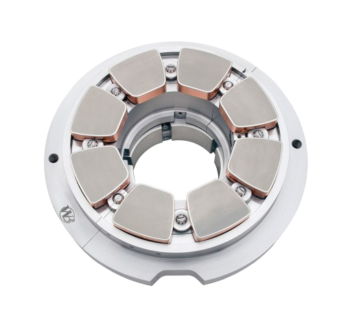
Fluid bearings are an advanced type of bearing that operate without solid-to-solid contact. Instead of rolling elements like balls or rollers, these bearings use a thin layer of fluid (either gas or liquid) to support the load, drastically reducing friction and wear. The fluid forms a pressure layer, which separates the bearing surfaces and provides lubrication.
- Key Features:
- Near-zero friction: Fluid bearings eliminate almost all friction since the surfaces are not in direct contact.
- Low wear and long life: Because there’s no physical contact between surfaces, fluid bearings experience little to no wear.
- High-speed capability: These bearings can function at extremely high rotational speeds, far beyond the capabilities of traditional mechanical bearings.
- Common Applications:
- Turbomachinery: Fluid bearings are used in high-speed applications such as turbines, compressors, and pumps, where the elimination of friction is essential.
- Hard Disk Drives: Modern computer hard drives often utilize fluid bearings to reduce noise and heat during operation, enhancing performance.
- Aerospace and defense systems: Given their high reliability and long operational life, fluid bearings are employed in critical applications like gyroscopes and spacecraft equipment.
- Why Choose Fluid Bearings?
- Fluid bearings are ideal for applications where high precision, longevity, and quiet operation are paramount. Their ability to function at high speeds and carry substantial loads with minimal friction makes them a top choice in fields requiring sophisticated machinery, including aviation, energy generation, and high-tech manufacturing
8. What are Linear Bearings 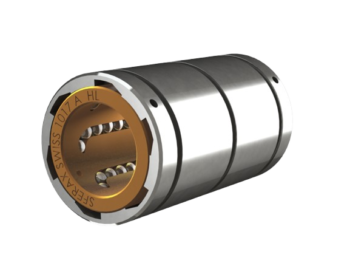
Linear bearings are quite different from roller and tapered roller bearings, as they allow motion along a straight line rather than rotational movement. These bearings are specifically designed for linear motion systems, where components need to move smoothly along a guided path. Instead of rotating, the bearing supports moving parts in sliding or rolling linear motion, typically used in precision systems like CNC machines, 3D printers, and robotics.
- Key Features:
- High precision: Linear bearings provide accurate, controlled movement along a straight axis.
- Low friction: Like rotational bearings, linear bearings minimize friction to ensure smooth motion, reducing wear and tear on components.
- Variety of designs: These bearings come in several forms, including ball-based linear bearings and roller-based linear bearings, which vary in load capacity and smoothness.
- Common Applications:
- CNC Machines: In the manufacturing industry, linear bearings are used to guide tool movements for precise cutting or shaping.
- Medical Equipment: Medical devices like imaging machines and surgical robots rely on linear bearings for controlled, smooth motion.
- Robotics: Many automated systems, including robotic arms, utilize linear bearings for accurate, repeatable movements in assembly lines.
Linear bearings play a crucial role in any machinery or system where precision linear movement is required. Their low friction and high accuracy make them ideal for precision machining and automation technologies
Conclusion
Bearings are the unsung heroes of machinery, allowing systems to function with minimal friction and maximum efficiency. From ball bearings in everyday consumer goods to magnetic bearings in high-tech aerospace applications, each type of bearing serves a unique purpose tailored to the specific needs of different industries. When selecting bearings for precision machining, understanding the specific load, speed, and environmental requirements is crucial for ensuring optimal performance and longevity of the machinery.
At Range Precision Machining, we understand the importance of selecting the right bearing for the job. Our deep expertise in precision machining ensures that every component, including bearings, is optimized for your specific application, delivering unparalleled performance and durability.