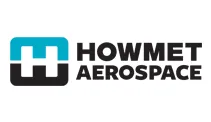
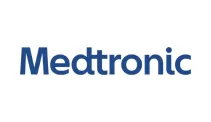
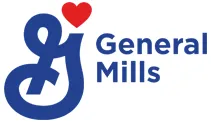
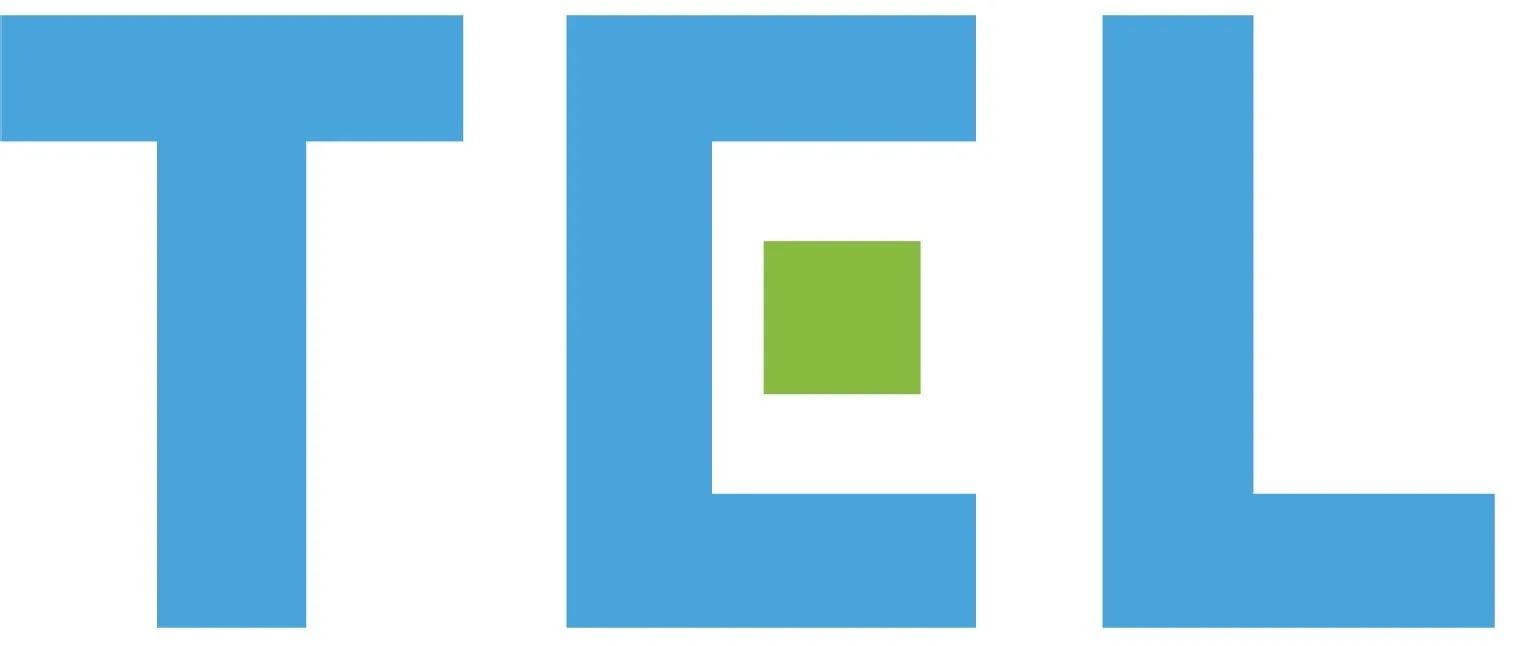
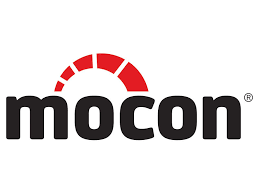

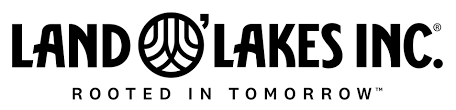
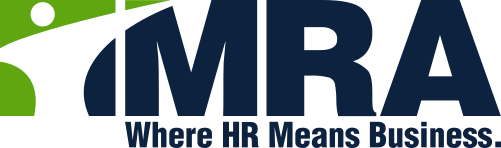

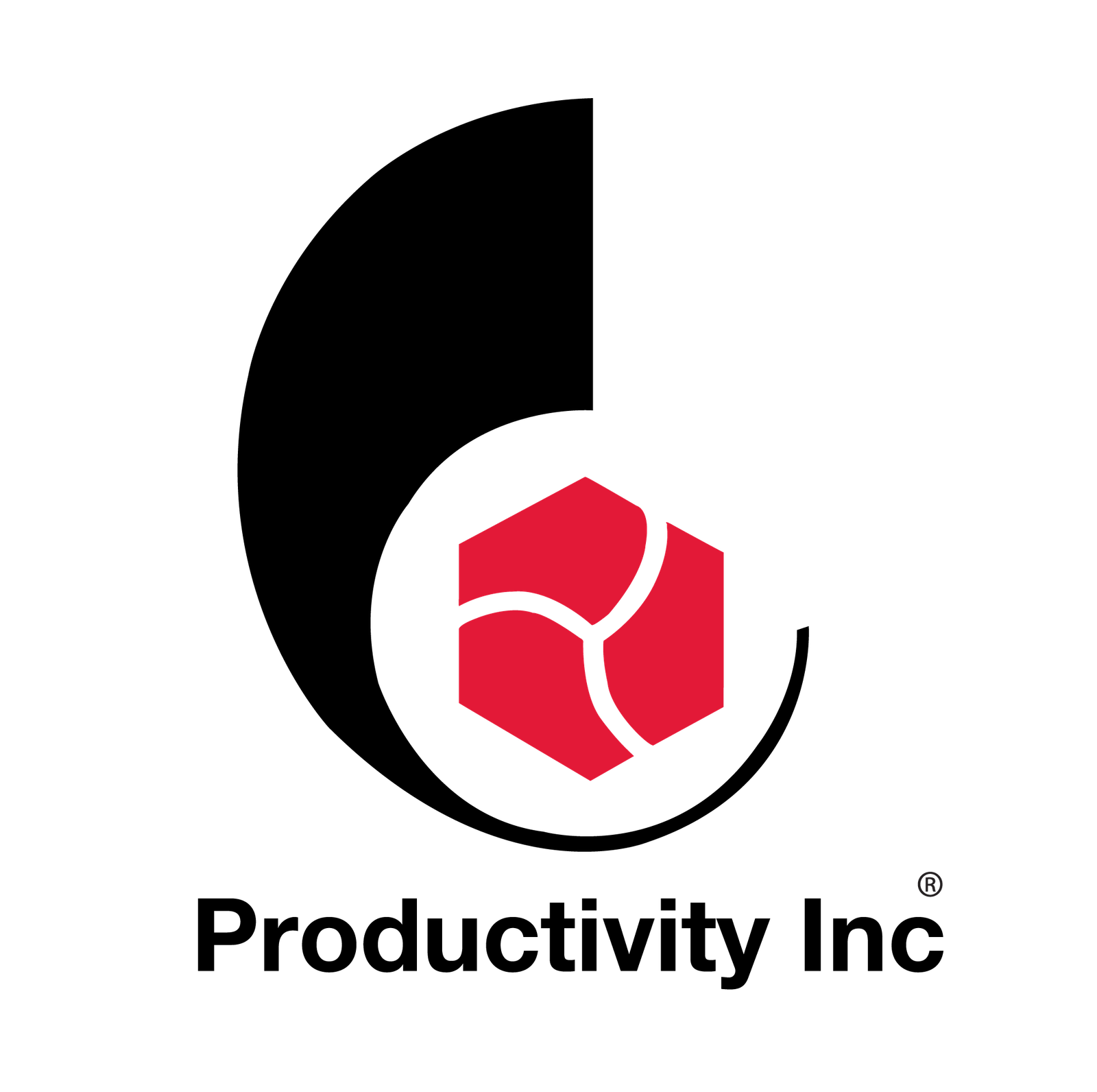


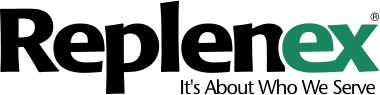
Value engineering aims to maximize value for all stakeholders by striking an ideal balance between cost and quality in product design and manufacturing.
We offer value engineering services to help our customers maximize their product's worth while minimizing manufacturing costs, drawing on four decades of experience and a team of highly qualified product engineers.
Our primary objective when starting a relationship with a new customer is to establish a solid foundation of trust and collaboration. Our clients are confident that they can rely on us for complete support across all phases of project development, production, and management.
Value engineering is a structured approach that focuses on maximizing the value of a product by optimizing its design, production processes, and material usage. It seeks to balance cost and quality to deliver products that offer exceptional value to stakeholders. This approach is particularly effective in manufacturing, where even small efficiencies can lead to significant cost savings without compromising quality or performance.
With more than 40 years of machining experience and a team of skilled product engineers, we embrace value engineering principles in every project. We work closely with our customers to deliver high-quality components swiftly and at competitive prices. This collaborative approach enables us to identify opportunities for cost reduction and process improvements, ensuring that our solutions meet the exact needs of our clients while adhering to strict quality standards.
Throughout this process, we never compromise on functionality, performance, reliability, durability, or safety. Instead, we use our expertise to create components that are both efficient and robust, providing customers with a product they can trust. Our commitment to value engineering ensures that we not only meet but often exceed expectations, establishing long-lasting relationships built on trust and proven results.
Throughout this process, we never compromise on functionality, performance, reliability, durability, or safety. Instead, we use our expertise to create components that are both efficient and robust, providing customers with a product they can trust. Our commitment to value engineering ensures that we not only meet but often exceed expectations, establishing long-lasting relationships built on trust and proven results.
Ensuring quality products through carefully selected materials, optimized processes, and streamlined project flow.
In the heart of a bustling factory, the journey of a product begins with the selection of materials. This is where value engineering takes center stage. The team meticulously evaluates each material, weighing its strengths and weaknesses to ensure the final product’s durability, performance, and aesthetics. Alongside the materials, they select the appropriate machinery to transform these raw components into something remarkable. Surface treatments, heat treatments, and coatings are the secret ingredients that enhance the product’s resilience and visual appeal.
Once the materials and machinery are chosen, the focus shifts to the factory floor, where the production process unfolds. Here, the value engineering team examines each step in detail, like detectives uncovering clues to optimize efficiency. They identify inefficiencies, redundant actions, and bottlenecks that could hinder production or increase costs. It’s a careful balance, with every move aimed at streamlining operations while maintaining quality. By refining auxiliary procedures, such as surface treatments, the team ensures that quality is upheld, even as they work to reduce costs. The goal is a leaner, more efficient process that delivers value.
The final piece of the puzzle is the project flow—a meticulously designed sequence of operations that ties everything together. The team orchestrates the entire process, from raw materials to the finished product, with the precision of a symphony conductor. They consider the best assembly techniques, optimal labor distribution, and effective quality control measures. Each step must seamlessly connect to the next, creating a smooth and efficient workflow. The objective is to achieve high-quality products at a reasonable cost. By minimizing unnecessary steps and ensuring a fluid process, the team creates a production flow that benefits both the company and its customers. The result is a production line that embodies innovation, efficiency, and exceptional value.
Our approach to value engineering and analysis is built on three key principles designed to assess the necessity of each component. We focus on achieving a balance between cost, quality, and timely delivery, ensuring that every part in a design meets its intended purpose without falling into over-engineering. Here’s how our process works:
During the design phase, many components are redundant and unnecessary. Our value engineering team thoroughly reviews each part to determine its relevance to the core function of the product. If we find elements that don’t contribute to the essential purpose, we suggest eliminating them, helping to streamline your product and reduce costs.
In the early stages of development, various parts like adapters, plates, bushings, and brackets are often included to make the product work. Our engineers take a holistic look at these designs from a manufacturing perspective. They seek opportunities to combine parts, reducing complexity and leading to a more efficient production process. This simplification often results in significant cost savings and a smoother assembly process.
For parts that can’t be eliminated or combined, our focus shifts to optimization. This involves exploring modular sub-assemblies, finding effective ways to join parts, and simplifying the final assembly through better part orientation. These steps ensure that your design is easier to produce, ultimately saving time and resources.
Range Precision, offers tailored machining consulting, expertly guiding clients through material selection, machining processes, and finishing methods to ensure optimal quality and cost-efficiency.
Range Precision offers tailored machining consulting, expertly guiding clients through material selection, machining processes, and finishing methods to ensure optimal quality and cost-efficiency.
With the right material choices in place, we then focus on identifying the optimal CNC machining systems and finishing methods to deliver the precision, volume, and cost efficiency you need. At Range Precision, “consulting” is more than just a word—it’s a core aspect of our service, ensuring you start your part-program with expert advice and a clear path to success.
With the right material choices in place, we then focus on identifying the optimal CNC machining systems and finishing methods to deliver the precision, volume, and cost efficiency you need. At Range Precision, “consulting” is more than just a word—it’s a core aspect of our service, ensuring you start your part-program with expert advice and a clear path to success.